Tunnel planning and design
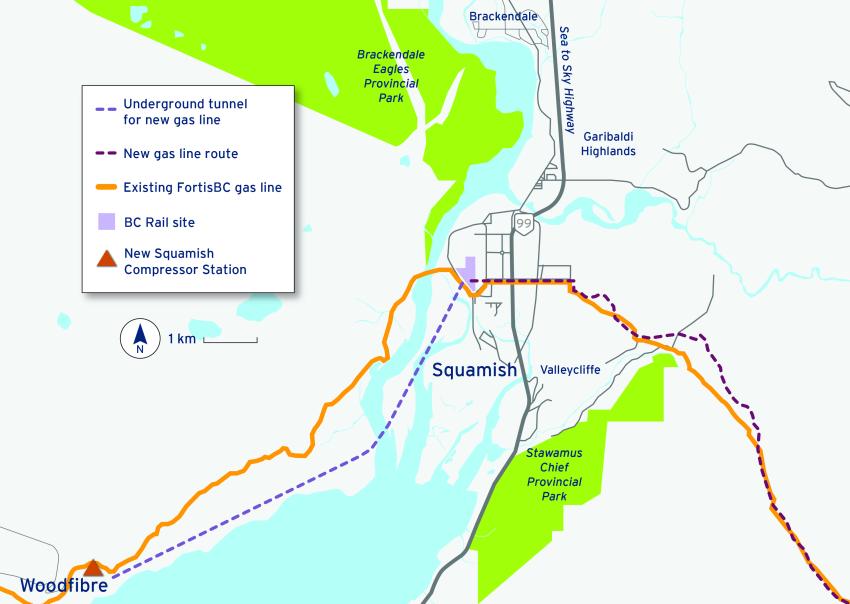
Our initial application to the BC Environmental Assessment Office (BC EAO) contemplated an overland route that would have required ground disturbance in the Skwelwil'em Squamish Estuary. As early engagement and project planning continued, Skwxwú7mesh Úxwumixw(Squamish Nation) expressed the importance of no surface impacts to the Skwelwil'em Squamish Estuary, given its cultural and environmental importance. As a result of the feedback from Skwxwú7mesh Úxwumixw, we amended the initial application to include a nine-kilometre tunnel beneath the Skwelwil’em Squamish Estuary Wildlife Management Area. In 2016, the EGP Project was approved by both the BC EAO and Skwxwú7mesh Úxwumixw after a separate, and extensive environmental review process. A condition of approval by both the BC EAO and Skwxwú7mesh Úxwumixwis that there will be no surface or industrial impacts to the Skwelwil'em Squamish Estuary. The nine-kilometre tunnel will extend from the Woodfibre LNG site to the BC Rail site in Squamish, passing under Monmouth Mountain and approximately 25 metres below the Skwelwil'em Squamish Estuary.
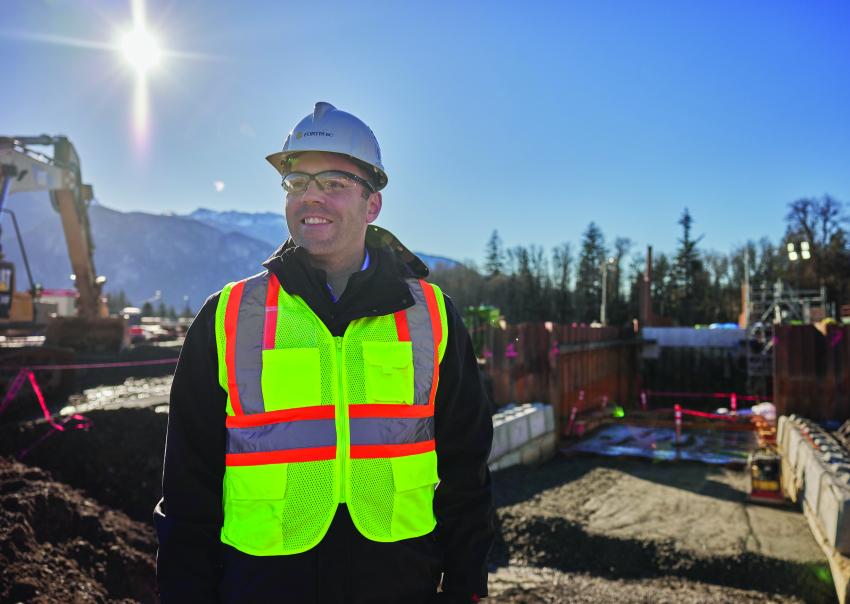
FortisBC project director Darrin Marshall joined the EGP Project team in 2018. He says, “Early in the planning process, we surrounded ourselves with geotechnical and tunnel experts, including a technical review panel from industry to help with our tunnel planning and design.”
Tunnel engineering specialist Ignacio Calvo González brought more than 20 years of tunnel-building experience to the project when he joined the EGP Project team as project manager in 2022. He observes, “One of the reasons this tunnel is unique is due to its diverse geotechnical conditions. For most tunnel boring machine (TBM) projects, you have a single, very specialized boring machine to deal with one specific type of geological condition. For this project, we needed two very different, specialized boring machines. The hard rock under Monmouth Mountain and soft ground under the Skwelwil'em Squamish Estuary means going from one geological extreme to another—all within the same tunnel—and each requiring its own solution. Our contractor has assembled a team who have recent experience working in these local geotechnical conditions and who have the specific technical expertise needed to tackle this unique challenge.”
Tunnel research
The team drew inspiration and knowledge from existing tunnelling projects both locally and around the world. The EGP tunnel isn’t the first tunnel to be built near Squamish using a TBM. The Ashlu Creek Hydro Project was successfully excavated more than 10 years ago.
“We learned from the success of other tunnel projects, as well as the challenges they faced,” Darrin notes. “For example, the Corrib Gas Pipeline Tunnel off the northwest coast of Ireland helped with our decision to use a decline structure to launch our TBM on the estuary side, rather than a shaft. It meant we could lower the TBM into this rectangular in-ground structure, which helps reduce groundwater from entering the tunnel. We also looked at the Gasduc III Pipeline Tunnel in Brazil, and the Romerike Tunnel in Norway to help inform other aspects of building the tunnel.”
Tunnel boring machines
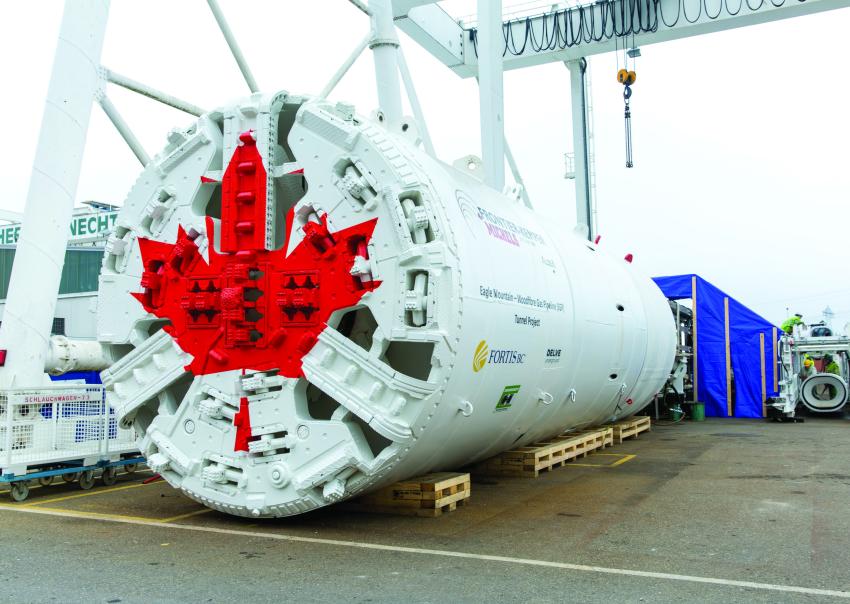
To facilitate the tunnel boring process, we commissioned two TBMs from Herrenknecht, one of the top tier tunnel equipment manufacturers in the world. The machines are tailor-made for the specific geotechnical conditions they’ll be tunnelling through: the soft ground TBM is designed to deal with largely soft, near uniform conditions under the estuary; the hard rock TBM is designed to tunnel through the granite under Monmouth Mountain.
Protecting the environment during construction
We’re committed to delivering our projects in an environmentally responsible manner. Our search for the best possible solution to protect the Skwelwil'em Squamish Estuary included engaging with Skwxwú7mesh Úxwumixw. Ultimately, we landed on a tunnel solution beneath the estuary.
Darrin explains, “Because of our determination to protect the environment and our commitment to Skwxwú7mesh Úxwumixw and the Squamish community, we adopted the tunnel approach to house the gas line. A solution of this scale would have been difficult to justify from a purely economic lens, but from a values perspective, the tunnel is a reflection of many of our core beliefs: Reconciliation, environmental protection and community engagement. Ultimately, that's why we're building it."
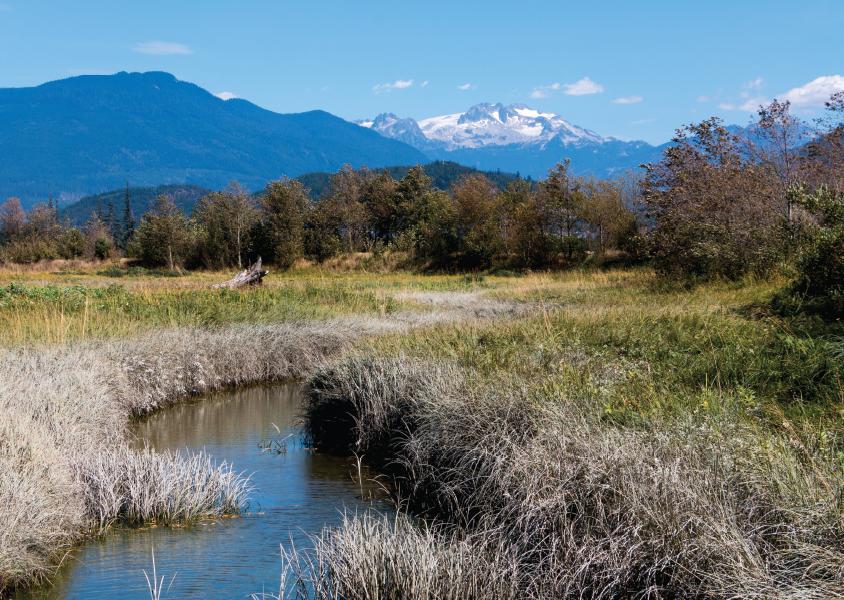
While the tunnel itself is the main form of environmental protection by avoiding surface impacts, we’re taking further steps to ensure our work approximately 25 meters underground is carried out with the environment top of mind.
Soft ground protection measures, 3.5 km of tunnel about 25 metres below the estuary
The team expects to encounter soft silt and clay within the approximately 3.5-kilometre section of tunnel on the estuary side. Measures will be put in place to ensure that the water from Howe Sound stays out of the tunnel. “As the soft ground TBM moves forward, we’ll install a tunnel support at the same time to maintain the integrity of the tunnel,” says Ignacio. “The specialized lining made of pre-cast concrete segments will be bolted together, creating a water-tight connection, completely sealing the tunnel off from the soil and water in Howe Sound.” This proven technology is common practice. Locally, it was used to build SkyTrain’s Canada Line underneath False Creek.
The soft, fluid-like consistency of the soil requires an additional containment measure. “To maintain a constant, even pressure on the face of the TBM as it moves forward, we need to use a slurry mixture made of bentonite clay,” adds Ignacio. “The slurry mixture blends with the excavated material, allowing it all to be pumped back to the BC Rail site, at which point the slurry and the excavated materials are separated. The slurry is reused and any water resulting from this process is either reused or treated.”
Hard ground protection measures, 5.5 km of tunnel under Monmouth Mountain
Within the 5.5-kilometre section of the tunnel under Monmouth Mountain, the team expects to encounter mainly coarse granite. Because the ground on this side is so hard, the tunnel will keep itself stable and won’t require an additional lining like the soft ground side. However, there may be large lineaments, or fractures, in the rock that must be managed while tunnelling is underway to prevent water inflow and rock instability. “All groundwater management will be conducted proactively,” says Ignacio. “We’ll probe ahead to determine where the groundwater is. Then we’ll inject high-pressure grout, so it can work its way into the lineaments, creating a barrier and sealing the tunnel against any large water inflows.”
Tunnel alignment
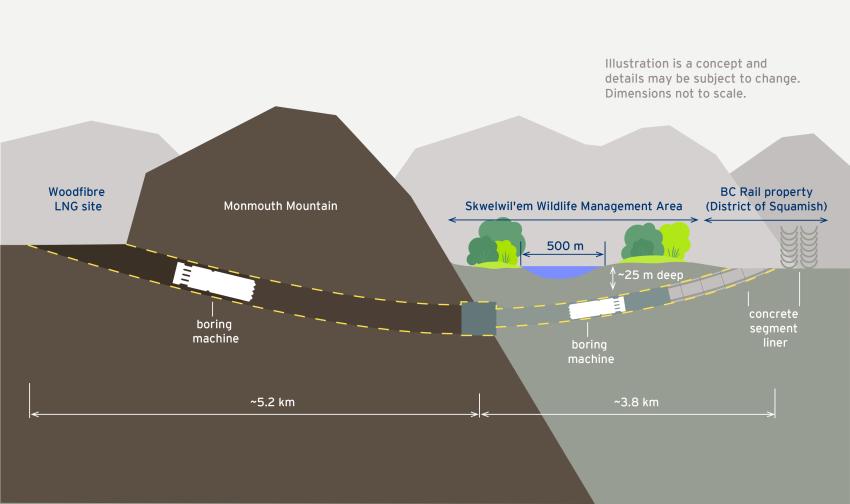
As the TBMs progress underground toward each other, they’ll constantly transmit data to the team about their location and performance. “The TBMs are equipped with world-class equipment, so we’ll have a constant idea of where they are,” says Darrin. “TBMs don’t move very rapidly. In some cases, it’s only a couple of centimetres per minute. We’re able to make continual adjustments or stop the machines entirely if required, and as needed based on their positioning.”
“As the hard rock TBM approaches the end of its section, we’ll stop it before it breaks through to the soft ground section. We’ll pull the machine back, and the team will excavate a small chamber. We’ll then have the soft ground TBM excavate through from the opposite side into the chamber.”
Proactive approach to planning supports safety
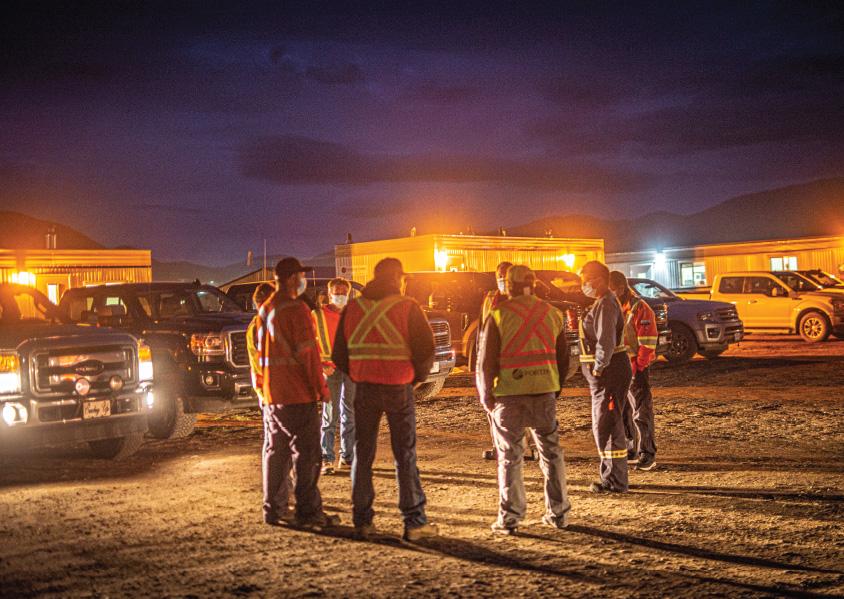
Safety is at the core of everything we do every day and is woven into our projects in the planning stages. Darrin notes, “We’re a risk-averse company. Our core philosophy is to do things safely and in an environmentally responsible manner, which includes taking a proactive approach to project planning. We look to identify the risks and challenges ahead of time, we address whatever we can in advance and we strive to have plans in place for any unanticipated outcomes.”
The EGP Project will expand a portion of our existing gas transmission system to provide natural gas service to the Woodfibre LNG facility in Squamish. It involves adding about 47 kilometres of new 24-inch pipe between Coquitlam and Squamish, and an additional three kilometres near Westwood Plateau in Coquitlam.